Automotive

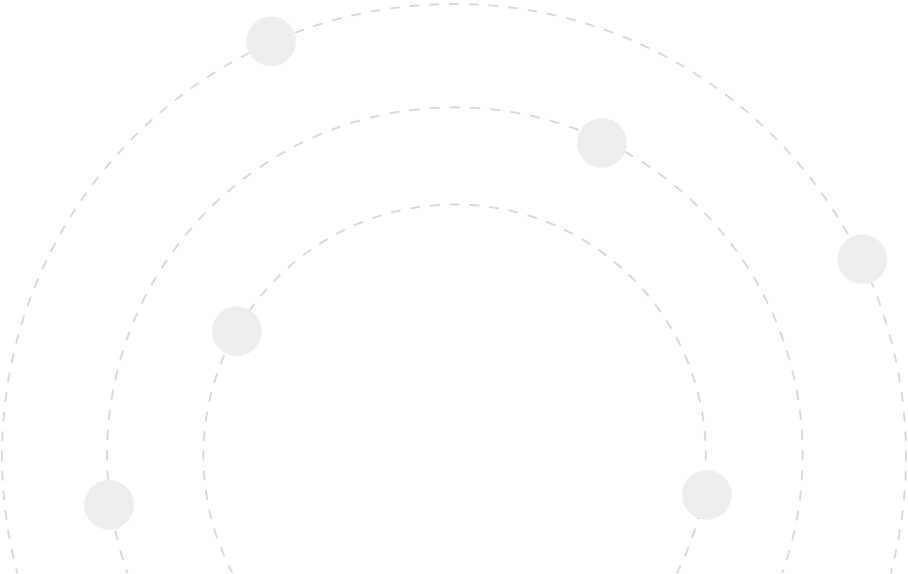
Market Trends
The automotive industry is built on precision, speed, and relentless innovation. But behind the sleek designs and powerful engines is a workforce facing tough conditions. Long hours, exposure to hazardous materials, faster production cycles and increasingly complex workflows.
Yet, the industry’s strength lies in its people. Keeping them safe means creating a workplace where they can perform at their best, confident that their well-being is a priority. As the industry accelerates into the future, companies must adopt advanced safety practices and proactive health management to protect their most valuable asset: their people.
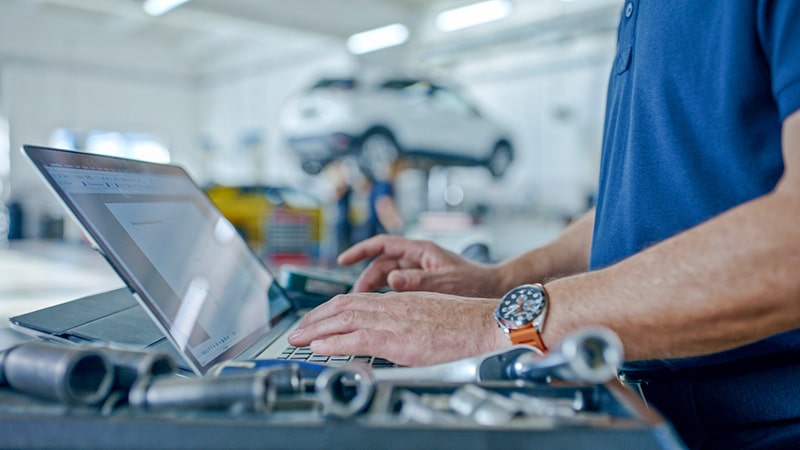
Rise of Comprehensive Safety Management Systems: Advanced platforms are integrating safety assessments, absentee management and human-centric safety analytics to improve workplace health outcomes.
Health Data Integration and Wearable Technology: Wearable devices are tracking worker health metrics like fatigue, posture, and vital signs, allowing early interventions.
Health Risk Analytics and Predictive Modelling: Predictive analytics are being used to identify high-risk workers based on health data trends, allowing targeted safety interventions.
Digital Wellness Platforms and Mental Health Support: Companies are adopting digital wellness platforms that offer mental health resources, stress management tools, and well-being assessments to support worker wellness and productivity.
Automated Compliance Audits and Safety Checks: Digital audit tools are automating safety inspections and compliance checks, reducing human error and ensuring adherence to safety standards.
Challenges
Data Silos and Integration Issues: Health data is often stored in separate systems, making it difficult to consolidate and analyse for comprehensive safety insights.
Lack of Customisable Workflows: Rigid occupational health systems do not adapt to the unique needs of automotive manufacturing processes
Reactive Health Management: Occupational health processes are typically reactive rather than proactive, leading to delayed interventions and higher injury rates.
Poor Communication Across Teams: Ineffective communication between health, safety and HR departments delays response times and affects employee well-being.
Manual Compliance Tracking: Tracking compliance manually increases the risk of errors and makes it difficult to keep up with changing safety regulations.
Limited Employee Engagement: Employees often feel disconnected from occupational health processes, leading to underreporting of health concerns.
Complex Return-to-Work Processes: Coordinating return-to-work plans for injured employees is complicated without centralised health data and communication.
Underutilisation of Digital Health Tools: Despite the availability of digital health tools, many companies still rely on outdated systems, impacting efficiency and safety.
What Can Be Done?
Automate workflows: EHR systems streamline scheduling, recordkeeping, and reporting, saving time and reducing errors.
Centralise data: Integrate occupational health data with HR and safety systems for holistic employee health insights.
Proactive risk management: Utilise data analytics to identify potential hazards, predict risks, and implement preventive measures.
Increase efficiency: Reduce paperwork, faster processes, and improved data accuracy.
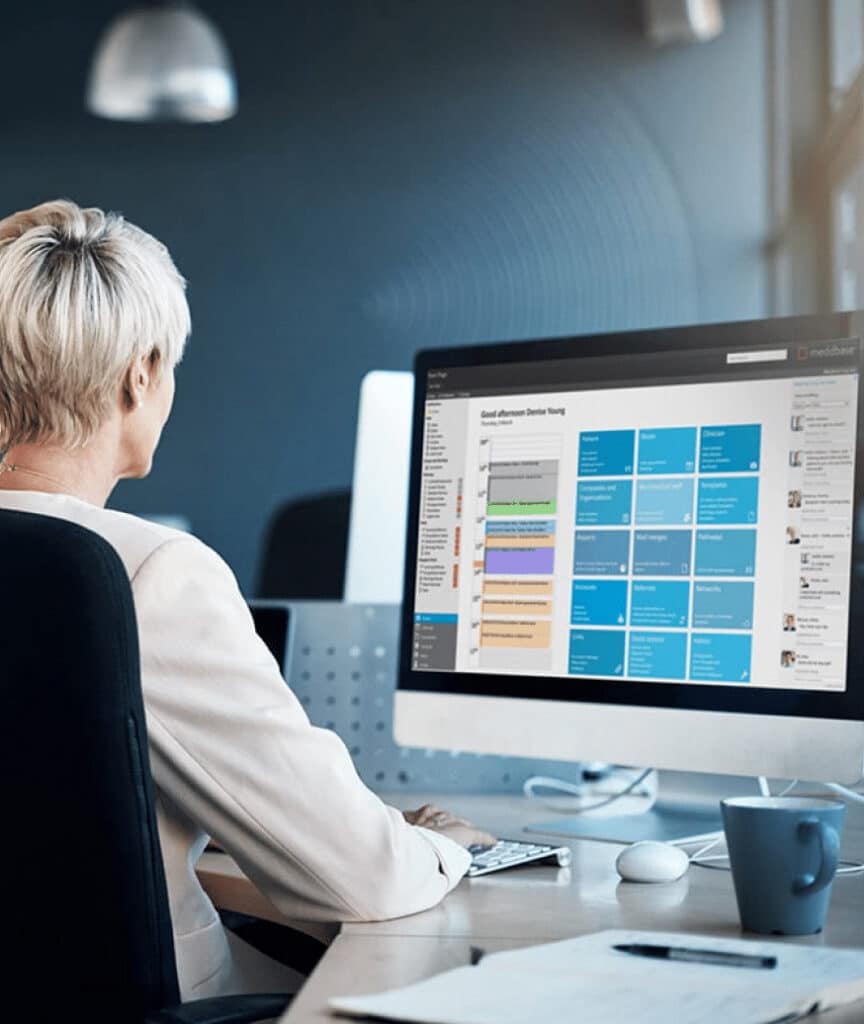
Enhance compliance: Streamline reporting and audit trails demonstrate regulatory compliance.
Improve risk management: Proactive identification and mitigation of potential safety hazards.
Better employee health: Early detection and management of health conditions, leading to reduced work stoppages and improved well-being.
Cost savings: Increase operational efficiency, reduced compliance costs, and improved employee health outcomes.