Logistics and Manufacturing

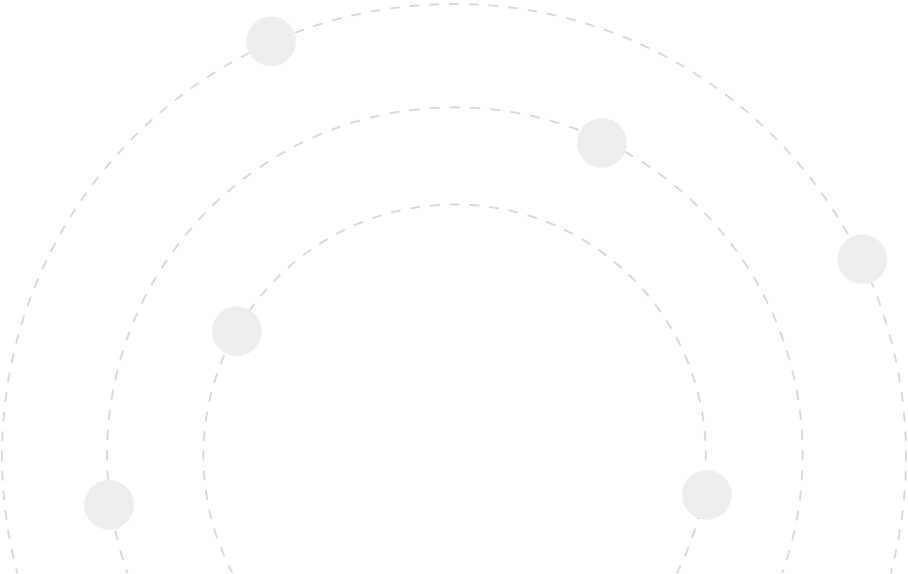
Market Trends
Logistics and manufacturing are vibrant but demanding fields, rife with physical risks like injuries and exposure hazards. Mental health concerns like stress and isolation also abound.
To thrive, companies must prioritise occupational health. This means proactive safety protocols, ergonomic workstations, mental health support, work-life balance initiatives, and regular health screenings.
Investing in employee well-being is not just ethical, but a strategic driver of success in a competitive landscape.

Rising workplace complexity: Increased automation, global supply chains, and diverse workforces raise unique health and safety challenges.
Evolving regulatory landscape: Stricter compliance requirements mandating proactive occupational health management.
Focus on employee well-being: Growing recognition of the link between employee health, productivity, and retention.
The Rise of Cloud-based EHRs: Cloud-based EHRs are gaining popularity due to their increased accessibility, scalability, and lower costs.
Interoperability: Interoperability between EHRs and other healthcare systems is becoming crucial for seamless data exchange and improved care coordination.
Leveraging EHR Data: Data is being monitored from EHRs to automate tasks and predict health risks.
Bridging the Distance: Telehealth solutions are being increasingly used for remote monitoring and consultations, particularly in geographically dispersed workforces.
Challenges
Data Silos and Integration Issues: Health data is often stored in separate systems, making it difficult to consolidate and analyse for comprehensive safety insights.
Lack of Customisable Workflows: Rigid occupational health systems do not adapt to the unique needs of automotive manufacturing processes
Reactive Health Management: Occupational health processes are typically reactive rather than proactive, leading to delayed interventions and higher injury rates.
Poor Communication Across Teams: Ineffective communication between health, safety and HR departments delays response times and affects employee well-being.
Manual Compliance Tracking: Tracking compliance manually increases the risk of errors and makes it difficult to keep up with changing safety regulations.
Limited Employee Engagement: Employees often feel disconnected from occupational health processes, leading to underreporting of health concerns.
Complex Return-to-Work Processes: Coordinating return-to-work plans for injured employees is complicated without centralised health data and communication.
Underutilisation of Digital Health Tools: Despite the availability of digital health tools, many companies still rely on outdated systems, impacting efficiency and safety.
What Can Be Done?
Automate workflows: EHR systems streamline scheduling, recordkeeping, and reporting, saving time and reducing errors.
Centralise data: Integrate occupational health data with HR and safety systems for holistic employee health insights.
Proactive risk management: Utilise data analytics to identify potential hazards, predict risks, and implement preventive measures.
Increase efficiency: Reduce paperwork, faster processes, and improved data accuracy.
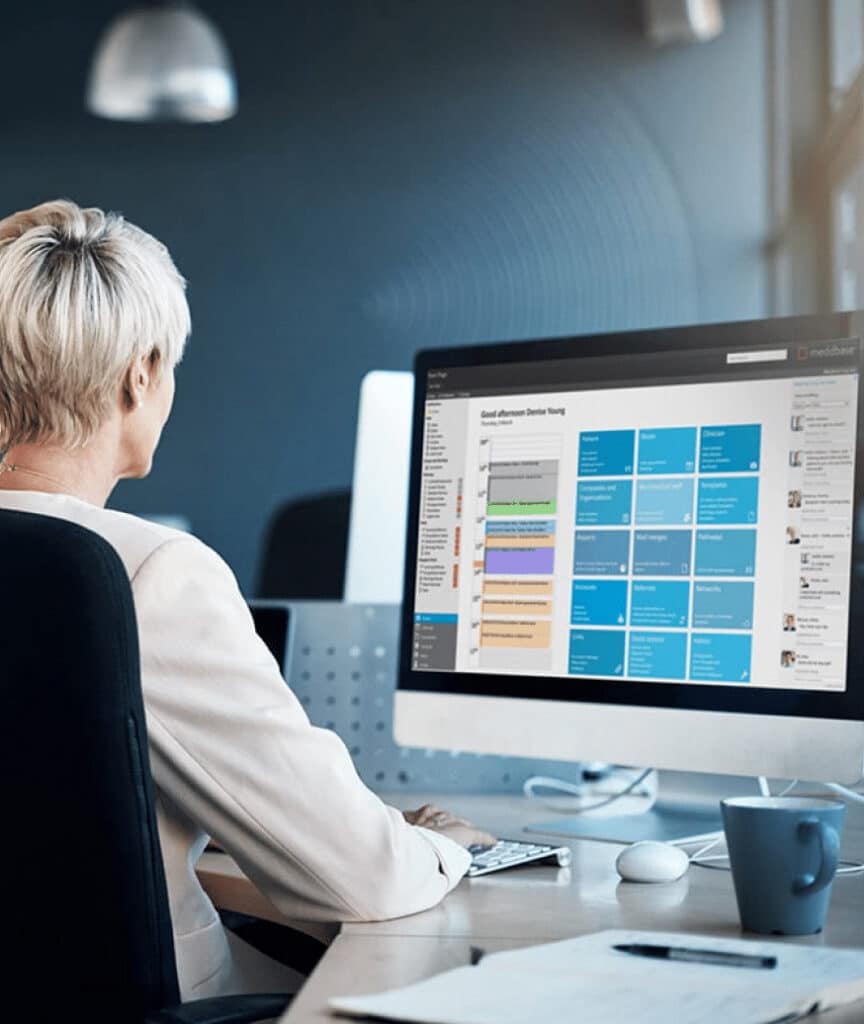
Enhance compliance: Streamline reporting and audit trails demonstrate regulatory compliance.
Improve risk management: Proactive identification and mitigation of potential safety hazards.
Better employee health: Early detection and management of health conditions, leading to reduced work stoppages and improved well-being.
Cost savings: Increase operational efficiency, reduced compliance costs, and improved employee health outcomes.